Unsere tägliche Arbeit basiert auf Prozessen, die wir definiert und installiert haben. Dabei spielt es keine Rolle, ob es sich um einen operativen Prozess, einen Verwaltungsprozess oder einen IT-Prozess handelt. Aber - wissen wir auch, wie unsere Prozesse täglich ablaufen? In ihrer Gesamtheit als auch im Detail? Überprüfen wir, ob unsere ursprünglichen Ziele mit den Prozessen erreicht werden? Suchen wir nach Verbesserungspotentialen? Prof. Axel Werner, Studiengangsleiter für Supply Chain Management am SRH Campus Hamburg, hinterfragt die Sicht der Unternehmen auf ihre Prozesse und zeigt Lösungsansätze auf.
Ausgangspunkt
Wenn in einem Unternehmen etwas produziert, verladen, gebucht oder bestellt wird, handelt es sich immer um einen Prozess, auch wenn das nicht in jedem Fall jedem bewusst ist.
In einem Unternehmen wurde sich überlegt, wie ein bestimmter Produktionsschritt, eine Bestellung ablaufen soll. Was sind die einzelnen Schritte? Wer muss was tun? Wer muss wen informieren? Was wird wie dokumentiert? Und, ganz wichtig: Was ist zu tun, wenn etwas nicht so abläuft wie geplant?
Woher wissen Mitarbeitende, die neu in ein solches Unternehmen eintreten, was sie in einem solchen Prozess tun müssen? In dem Fall haben es die zertifizierten Unternehmen (z.B. DIN/ISO9001) leicht, denn sie müssen fast alle Prozesse genau beschreiben und die Mitarbeitenden haben sich an die zu Beschreibung halten. Somit ist die Einarbeit theoretisch einfach: Wenn eine Aufgabe übernommen wird, so wird dazu eine Beschreibung der dazugehörigen Prozesse ausgehändigt, damit der Zuständige direkt anfangen kann zu arbeiten.
In der Praxis sieht es aber so aus, dass eine Prozessdokumentation weder vollumfänglich ist, also nicht alle notwendigen Prozesse umfasst, noch ist sie vollständig, das heißt, sie erfasst die Prozesse nicht im Detail in ihrem derzeitigen Stand. Das liegt unter anderem daran, dass ein Unternehmen – hoffentlich – nie statisch ist, sondern sich aufgrund externer und interner Anforderungen ständig weiterentwickelt. Zudem ist es sehr aufwendig, die entsprechenden Prozessbeschreibungen nachzuführen. Somit wird die Einarbeit schwierig. Typische Gesprächssituationen sind beispielsweise: „Warum führt der angegebene Link nicht zum nächsten Prozessschritt?“ „Ach, ja, da haben wir eine weitere Überprüfungsschleife eingebaut, da musst du zuerst folgende Aktion durchführen...“, oder: „Ich möchte die Palette mit der beschädigten Ware ins Sonderlager bringen, da ist aber der Zugang versperrt“. „Stimmt ja, das haben wir inzwischen verlegt – da musst du ins Nebengebäude fahren“.
Was zeigt dies?
Prozesse sollten den Kern einer jeden Unternehmensaktivität bilden. In Unternehmen sind sie in der Regel beschrieben, werden aber nicht konsequent nachgeführt, nicht ausreichend geschult, und vor allem nicht ständig überprüft und verbessert.
Es ist die Aufgabe des Managers und der Managerin oder des/der Prozessverantwortlichen, dafür zu sorgen, dass die Prozesse in Ihrem Verantwortungsbereich zum einen aktuell beschrieben sind, zum anderen aber auch ständig überprüft und verbessert werden. Sollte dies nicht der Fall sein, wird jede Menge Optimierungspotential verschenkt.
Was sollten getan werden?
- Prozesse einführen und genau beschreiben
- Mitarbeitende schulen
- Prozesse vor Ort regelmässig in jedem Detail überprüfen
- Prozesse auf Verbesserungsmöglichkeiten analysieren (MIT den Mitarbeitern)
- Prozesse in ihren Wechselwirkungen zu anderen Prozessschritten und zu anderen Prozessen überprüfen
Beispiel 1: In der Produktion von Getriebeteilen eines Automobilherstellers wurden Zahnräder gepaart, das heißt, in ihrem Zusammenwirken optimiert. Die so gepaarten Zahnräder wurden mit einer 4-stelligen Zahl markiert. Es gab aber immer wieder Verwechslungen und Zahlendreher bei der Eingabe der Zahlen, die dazu führten, dass die falschen Zahnräder kombiniert wurden, was zu Produktionsausschuss führte. Als Lösung wurden die Zahnräder statt mit Zahlen mit zufällig erzeugten vierbuchstabigen Wörtern gekennzeichnet. Damit wurde diese Fehlermöglichkeit fast komplett eliminiert.
Beispiel 2: Ein Unternehmen stellte seine interne Kommunikation auf eine neue Plattform um und schuf dort auch die entsprechenden Verteiler für größere Empfängergruppen. Es schaltete jedoch bereits Wochen VOR dieser Einführung die alten Empfängergruppen in MS Outlook ab, was dazu führte, dass eine Versendung von Nachrichten an mehrere Empfänger eine aufwändige händische Eingabe von E-Mail-Adressen erforderte.
Aus diesen Beispielen wird klar, dass alle Prozesse sich ständig im Detail angesehen werden müssen. Es muss stetig nach Verbesserungen gestrebt werden, sowie Fehlermöglichkeiten gesucht werden (um diese zu eliminieren).
Darüber hinaus sollten alle Prozesse aber auch ganzheitlich im Auge behalten werden; ganzheitlich heißt, dass über den einzelnen Prozess oder Prozessschritt hinaus die gesamte Prozess(schritt)kette und das Zusammenwirken der Prozesse analysiert werden müssen. Es kann sein, dass ein bestimmter, gut funktionierender Prozessschritt (Buchung / fehlende Buchung) negativen Einfluss auf einen nachgelagerten Prozessschritt nimmt. Zum Beispiel gibt es Buchungsseiten, bei denen nach einer abgeschlossenen Buchung nicht automatisch eine weitere Buchung möglich ist, sondern die komplette Information neu eingegeben werden muss um eine weitere Buchung durchzuführen. Dies scheint nicht von den verantwortlichen Managern vorher ausprobiert worden zu sein.
Jetzt ist bewusst WAS, aber es bleibt die Frage nach dem WIE!
Das Thema „Prozessoptimierung“ spielt in der Automobilindustrie seit jeher eine große Rolle. Die Kombination aus hoher Komplexität, einer enormen Anzahl an verschiedenen Varianten und großer Stückzahl macht es erforderlich, die administrativen und operativen Prozesse für die Fahrzeugproduktion sehr genau zu planen und ständig auf Fehlermöglichkeiten oder Verbesserungspotential zu analysieren. Dazu werden verschiedenste Werkzeuge verwendet.
Verbesserung heißt zum Beispiel, dass zwischen Wertschöpfung und Verschwendung unterschieden und versucht wird, letztere zu minimieren. Verschwendung wiederum ist definiert als alles, was „nicht direkt dem Kunden hilft“ und damit nicht unmittelbar dazu beiträgt, das Produkt weiterzuentwickeln oder die Produktion oder Logistik weiterzutreiben.
Ein Beispiel ist die Optimierung der – immer noch überwiegend – manuellen Montageprozesse. Während früher die Montagemitarbeiter weite Wege gehen mussten, um sich ihre Montagekomponenten (Lenkräder, Scheinwerfer und selbst die Räder) zu holen, sind die Prozesse heute so weit optimiert, dass die Mitarbeitenden am Band sich umdrehen, hinter sich die nächste Fahrzeugkomponente finden, sich wieder umdrehen und diese Komponente an das Fahrzeug schrauben oder klipsen. Die unproduktive Wegezeit, die reine Prozessverschwendung darstellt, wird fast völlig eliminiert und die Zeit der Montagearbeitenden zu fast 100% für Montagetätigkeiten genutzt. Die Regel dazu lautet: Nicht der Mensch geht zur Ware, sondern die Ware geht zum Menschen. Dass das wiederum den Aufwand für die Logistik erhöht, ist klar.
Im Lager kann eine solche Optimierung zum Beispiel heißen, einen Liefer-Lkw immer exakt auf dem Punkt zu parken, wo er für die Entladung und den Weitertransport von Paletten optimal steht. Dies verringert den Aufwand für den Staplerfahrer. Und damit wirklich jeder Lkw-Fahrende diese Parkposition findet, sollte sie auf dem Boden entsprechend markiert werden.
Das Werkzeug für diese Art der Prozessoptimierung heißt Wertstromanalyse. Die Prozessverantwortlichen und die Beteiligten folgen dem Materialfluss in einer Prozesskette und nehmen genau auf, was mit den Waren oder den Bauteilen passiert. Wo werden sie wie bewegt, wo liegen sie wie lange? Das Ganze wird mit einfachen Mitteln festgehalten, und anschließend werden Verbesserungsmöglichkeiten erarbeitet.
Woher ist schlüssig, dass Prozesse auch so ablaufen, wie sie ursprünglich optimiert wurden? Dies funktioniert nur durch Messungen. Es müssen die Ziele für die wesentlichen Parameter, z.B. Verladezeit, Lieferzeit, Qualität festgelegt werden und dann die Ist-Werte ständig erfasst werden. Bei Abweichungen muss sich der Prozess vor Ort angesehen und gemeinsam mit den Mitarbeitenden herausgefunden werden, wo die Ursachen für die Abweichungen liegen und wie die Mitarbeitenden unterstützt werden können, damit der Prozess verbessert werden kann. Das dazugehörige Werkzeug heisst Qualitätsregelkarte und bildet in der Automobilindustrie die Basis für jeden relevanten Prozess. Ein Beispiel wäre eine Vorgabe für eine Lkw-Ladezeit und dann eine ständige Messung, um das IST mit der Vorgabe vergleichen zu können. Dies wiederum setzt voraus, dass der Lkw reproduzierbar parkt – siehe oben.
Es gibt eine Vielzahl weiterer Methoden, um Prozesse zu analysieren und zu verbessern, und der SRH Campus Hamburg bietet Möglichkeiten, diese Werkzeuge – zum Beispiel im Rahmen einer Masterarbeit – bei Unternehmen aus der Logistik-Initiative Hamburg anzuwenden. Derzeit diskutiert die SRH eine solche Prozessoptimierung z.B. mit der SITRA Spedition, ist aber offen für weitere Unternehmen, die gemeinsam Prozesse ganzheitlich und im Detail analysieren wollen.
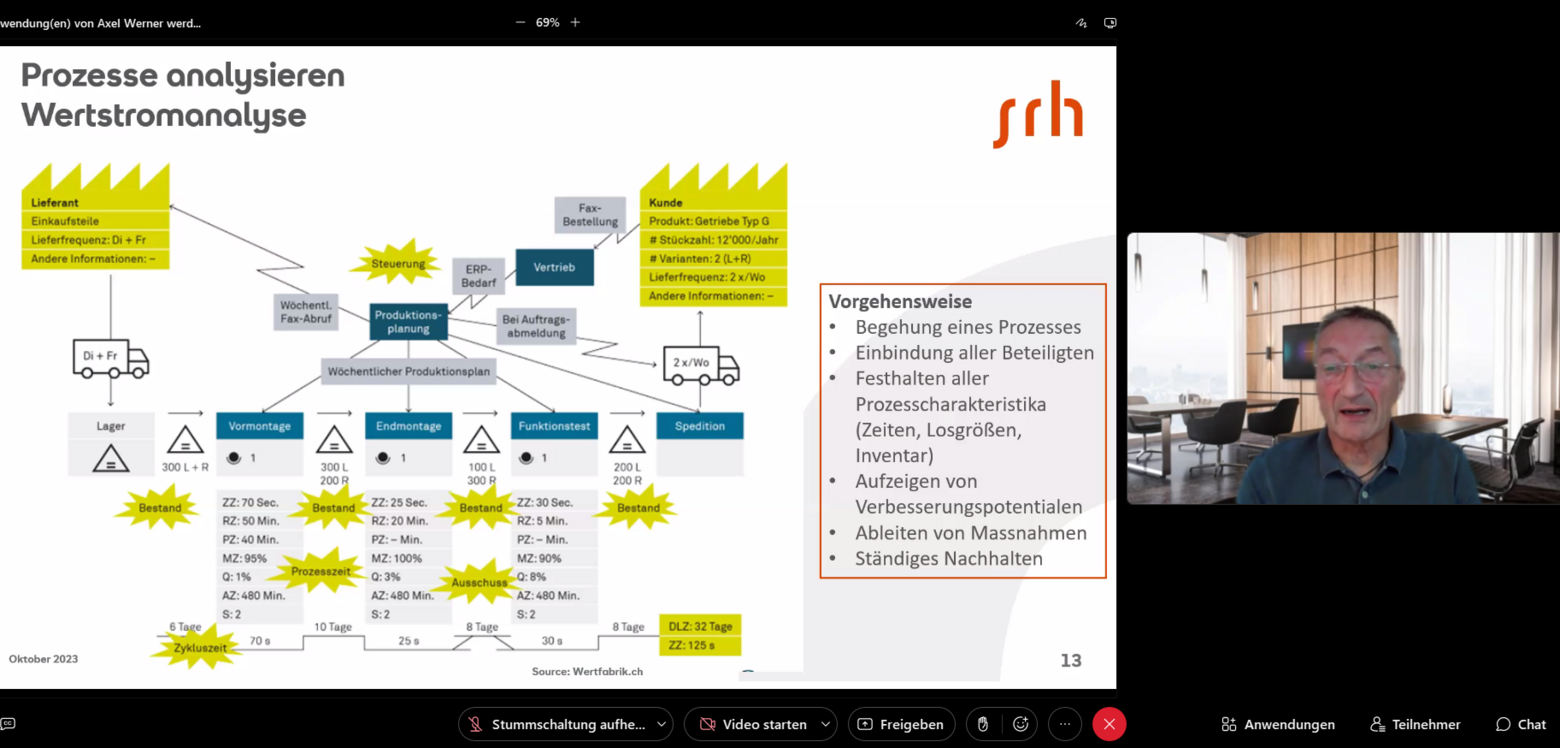
Titelbild: canva/aprott/getty images